sent to me by: Dave & Mary Lahar, Northeast Kingdom, VT, USA
4.6 m (15’) axial with power furling
26 m (85’) guyed tower
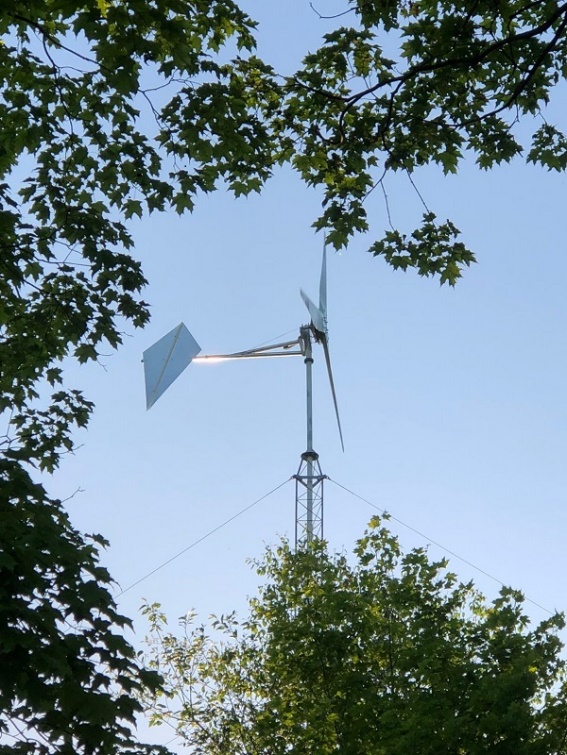
The furling actuator is mounted in the base of the tower. It is 12VDC, travels .46 m (18”) and is rated at 68 kg (150 lbs). It has a built-in potentiometer feedback allows for position control.
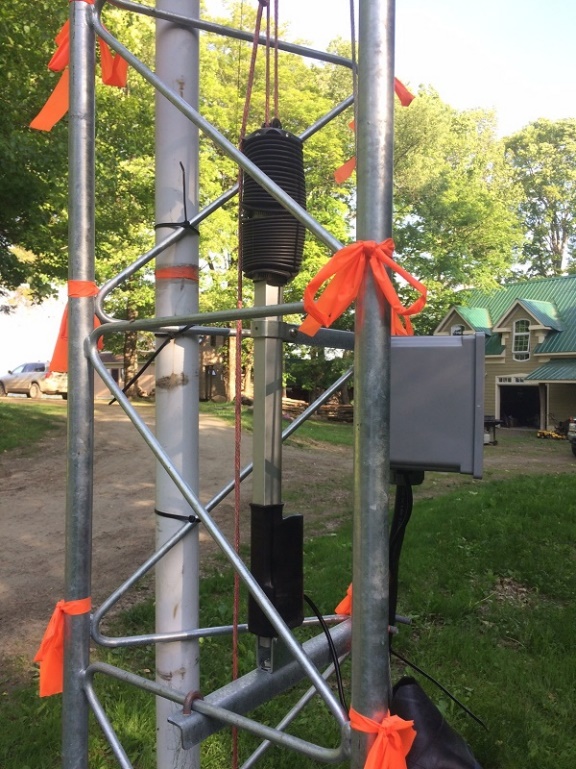
The actuator pulls on a 4 mm dyneema line to furl the tail through a pivoting snatch block, like those used on many PTO tractor winches. Dyneema is very strong, light-weight and has virtually no stretch. A small sash weight keeps the line taught, and the tail is free to furl independently.
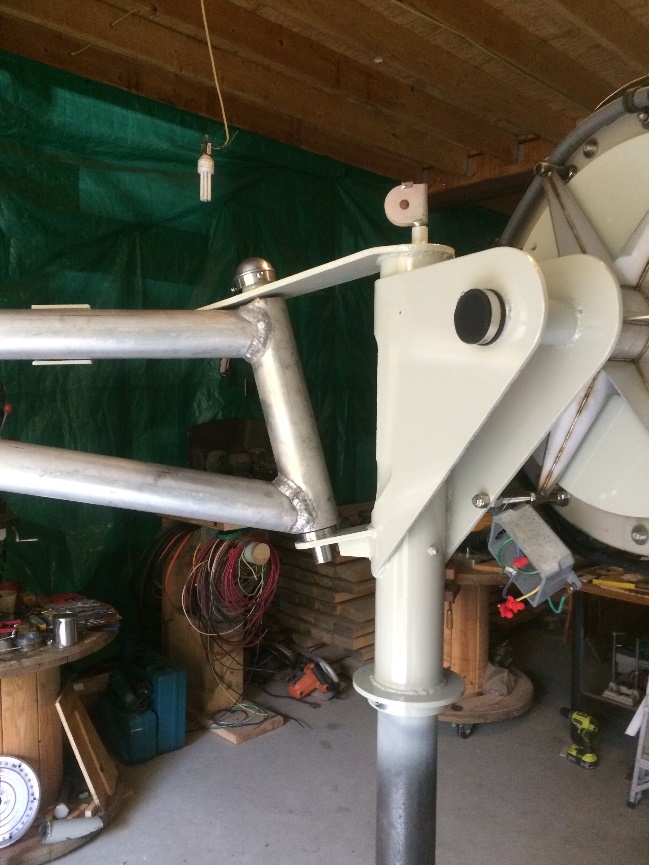
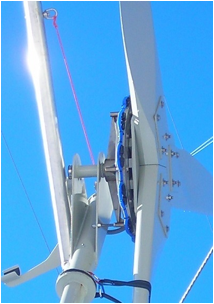
When the winds are predicted to be unusually high, or rough (or both), or when we have ample solar production we can easily shut things down manually. This is by far the softest method – furl the tail, and close in the (resistive) load bank – now we’re ready for most anything that comes our way.
The furling actuator is also controlled by the charge controller whenever the input voltage gets above a user-selected pre-set. It is a simple dry-contact relay action.
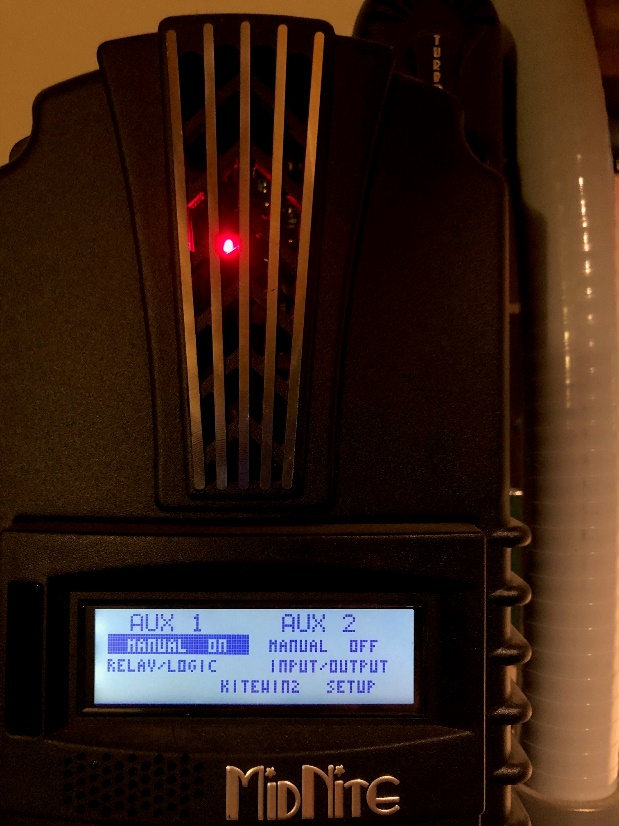
We originally had a small hand winch to operate the tail, and that worked fine. This arrangement allows things to be controlled from the house. When the wind gets unruly, as it regularly does, or the PV is ample for the loads, it is nice to be able to save the wear and tear on the turbine. The actuator has been in place now for about two years and has worked very, very well for us.
Thanks again for all your inspiration and we hope this may be of use to some of your readers.
Sincerely, Dave & Mary
Thanks for the pictures and info. I found a marine (Holts) stainless steel block in my kit this AM so I’ve spent the morning removing the jamming cleats and fitting the block on to some tube so it can swivel on the top of the alternator frame.
Thanks again
Just to clarify the picture – it is rigid PVC conduit coming up on the outside of the tower (about 6 m). This is the line from the house. It terminates in a metal box that holds the twist-lock receptacle. From there it transitions to the SO cord (black looped cord) up the inside of the tower. This cord has rubber sheathing and stranded wire and is very flexible. It can twist many (20 or 30 maybe?) full revolutions before it would be a problem, and the dyneema line, which is a single braid rope, slides easily about the electrical cord.
Interestingly, I worked for an induction wind company in the late ’70s/early 80s, and they went to twist cords like this to avoid sliprings, and their associated cost and maintenance. Some were on 40kW units!
Kindly, Dave
Hi Andy,
We have just one heavy SO cord (#6-4, CU) running down the center of the tower. There are no slip-rings, just this “twist cable” as some call it. The dyneema line is right next to this cord. There a strain-relief on the top and we have a 50A twist-lock plug and recepticle at the bottom that allows us to untwist the cord, as you would do with, or without, the furling line. We probable do this every three months or so.
Here is the picture that David just sent me. As it is a rigid cable it cannot accommodate many twists and so there is no need to put a sheath on the winch rope.
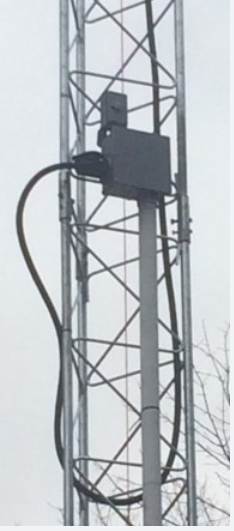
Cheers Hugh.
So basically the down haul is sleeved all the way down the tower/tube inside some reinforced nylon flexible piping. I shall do some research on the cable product they recommend.
I
Hi Dave and Mary. How do you avoid the (presumably 3) cables for AC out from the alternator becoming tangled in the actuator cable inside the tower/tube and potentially failing when needed. I have recently completed the build of a 4.5Mtr dia HP turbine and had considered something similar as a mechanical brake.
Hi Andy,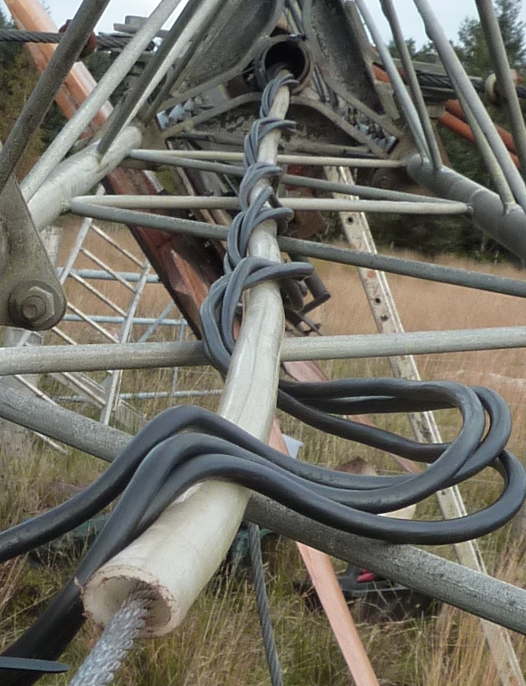
I passed the question on.
In my case here is a photo of how I did mine. My tail furling cable is steel wire rope which is a mistake as it only lasts a year or so before it frets away and snaps. I need to look into the special material mentioned in this story.
The combination of pipe and wires goes on up into a long plastic pipe beyond what you can see but it does need untwisting every year or so.
As for the tail furling winch it’s only something I need every five to ten years in a really scary blow, and by that time it has always fallen into disrepair.