Greg sent me some photos of the hydros he is building using axial flux alternators to provide direct single-phase AC for sites in Papua, Indonesia. Here is some information. Greg’s email is [email protected]
These are single phase units, 240VAC, 50Hz.
The first model (I made 6 units about 6 years ago) had magnets secured with a Stainless steel band and fibreglass epoxy. magnets are 60mm diameter. It is capable of up to 2.8kW (1000RPM). Measured efficiency was around 93%.
I started on 18 “Mark 2 machines” about 4 years ago, but life intervened and they have been on hold since. I’d be happy make a little report with a few more details if you think people would be interested.
The second model is still under construction, but utilises aluminium magnet keepers for more positive magnet security and better cooling air flow. I also did a bit of coil shape optimisation (magnetic field computer simulation). I have a 6 pole (1000RPM) and 4 pole(1500RPM) version. I calculate that these machines will be capable of 4~6kW maximum, partly due to larger magnets and lower coil resistance, but mainly due to better cooling.
My Mark 1 machines had both pelton and turgo turbine options. I used an Eco-innovation plastic pelton wheel for the high head sites, and two sizes of turgo turbine for lower head sites. I bought the buckets from [email protected] in Italy. My Mark 2 machines will also use three different turbine diameters to accommodate different head sites, but they will be turgo turbines only. I am thinking to make my own turgo buckets, possibly by 3D printing…
I went with circular magnets thinking they would give more sinusoidal voltage. Below is the design coil dimensions of my Mark 2, 6-pole generators. The magnets on this machine will be 70mm diameter running at a pitch circle of 88mm. According to the simulation, this gave the best compromise between high magnet flux capture and low copper volume with good sinusoidal waveform. I haven’t actually built one to test yet though.
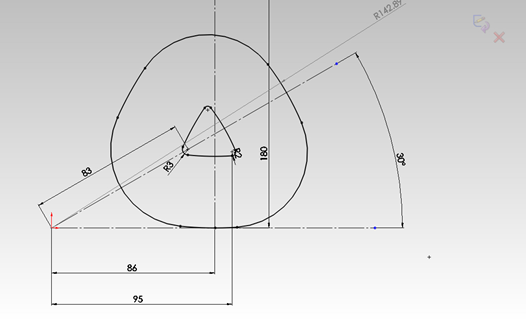
The machines are regulated with an electronic load controller (dump load controller). The ELC I am using regulate frequency (eg 50Hz). Voltage seem fairly stable as long as frequency is well regulated. (I am working on my own ELC actually, due to shortcomings with some commercial ones we have tried)
Hope you get some joy out of seeing the work of a fellow renewable energy enthusiast!
Bokondini from the air Mark-2-Turbine-Casing-fabrication Mark-2-Rotor-painting Mark-2-nozzle-blanks Mark-2-Generator-Casing-fabrication Mark-2-Assembled-tubine-generator Mark-2-Assembled-tubine-generator Mark-2-4-pole-rotor Mark-1-stator-casting Mark-1-Shipment Mark-1-rotor Mark-1-Low-head-version Mark-1-Generator Mark-1-Generator-casing Mark-1-Assembling-Generator-and-Turbine. 7-Eragayam-site 3-securing-the-casing
Hi Kostas,
Thanks for your kind comments and the informative links. I like the AFPM hydro machine you made, which looks like a very similar design to mine!
I will also explore the idea of using powder iron in the casting resing to increase magnetic permeability of the stator.
Regarding 3D printing the turbine spoons – I think I stumbled upon your paper some time ago and it inspired me to think about this for my project. Since resin printers recently became more affordable, I decided tor try making my turgo rotors with this technology. Here are some pictures of my first design – a 175mm PCD rotor to suit jets up to about 20mm.
https://drive.google.com/file/d/1mCEd57EnQHHyfGiooj656l-6l9wwvZWt/view?usp=sharing
https://drive.google.com/file/d/1BHEvV82PXBm033tgvtbL8ERuTh5TTMXZ/view?usp=sharing
I’m not sure whether resin or FDM printing is better for this application. The cost of resin is a little more than the filament, but resin can achieve quite smooth finish and strength is more isotropic. On the other hand, resin tends to have poorer impact energy and is degraded by extended UV exposure.
I will test this in the field soon, so it will be interesting to see if it is durable enough.
Would love to talk more about your electric power projects!
Greg
Hi Greg and Hugh,
Thanks for posting, this is all very interesting!
In 2013, I made pico-hydro installation using an axial flux permanent magnet generator, built as described in Hugh’s wind turbine manual, and driven by a plastic spoon turgo turbine. Here is a post scoraigwind.co.uk/2013/08/pico-hydro-in-greece/ and here is a video http://www.facebook.com/304122449642277/videos/vb.304122449642277/813566962031154/ It has been spinning without any maintenance for 7 years, so I have found it to be very reliable.
As it is a low power machine I don’t use an ELC, but use it in conjunction with a small battery bank and a 1.5kW inverter to get the power needed from the system.
Also here are some tests at the NTUA, to use a powder iron core in such pico-hydros ruralelectrification.files.wordpress.com/2019/02/comparison-of-coreless-and-soft-magnetic-composite-core-axial-flux-permanent-magnet-generators-for-locally-manufactured-pico-hydro-plants.pdf
Finally, in 2016 we printed the spoons using a 3D printer and tested them in the lab for efficiency with good results ruralelectrification.files.wordpress.com/2016/10/dopper.pdf
I still have not installed them at the site to test them for long term durability, but given they are very cheap and easy to print, I would assume that they would be a good low cost and locally made alternative to plastic cups, although they might need to be replaced more frequently.
Thanks again for sharing!